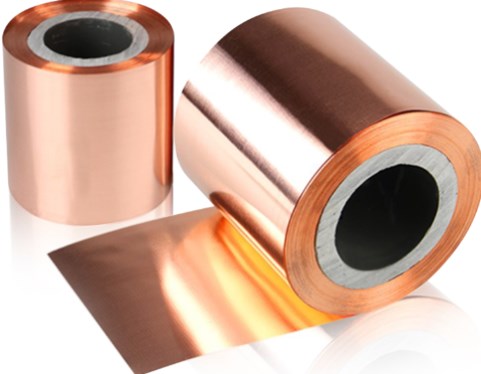
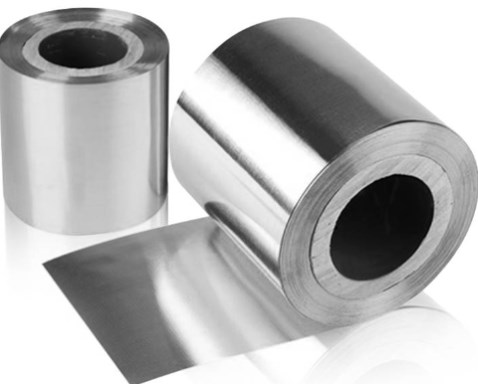
Aluminum foil and copper foil are highly favored and widely used current collectors in batteries, thanks to their numerous advantages:
1. Excellent Conductivity: Both aluminum foil and copper foil exhibit excellent conductivity. During electrochemical reactions, they facilitate the rapid conduction of electrons, thereby enhancing battery performance.
2. Flexibility and Durability: Lithium-ion battery electrode sheets are typically manufactured using stacking or winding processes, involving multiple cutting and slicing steps. This demands that current collectors be flexible and resistant to breakage. Aluminum and copper foils, with their soft texture, meet these requirements, allowing for both winding and stacking processes without the risk of brittleness or breakage.
3. Chemical Stability: Both materials are relatively stable in the air. Aluminum tends to undergo chemical reactions with air, forming a dense oxide film on its surface. This film prevents further oxidation of aluminum and provides a certain level of protection in the electrolyte. Copper, being inherently stable in the air, rarely undergoes reactions in dry air.
4. Cost-Effectiveness: Compared to most metals, aluminum foil and copper foil are cost-effective, and Earth's resources for these metals are abundant. This cost-effectiveness contributes to saving production costs in battery manufacturing.
Since the widespread use of lithium-ion batteries, the thickness of current collectors has been continually optimized. The thickness of positive electrode aluminum foil has decreased from the previous 16μm to the current 10μm, and in some cases, even 8μm. Similarly, the thickness of negative electrode copper foil has reduced from 12μm to 6μm, and in some instances, as low as 4/5μm. As the thickness of current collectors decreases, the battery's overall thickness and volume also reduce, promoting an increase in battery energy density.